We have so much amazing material surrounding us that we take its greatness for granted. Perhaps you have closely examined the steel buildings that are now our churches, schools, and fire departments? Because these gigantic steel girders blend to their surroundings, they are generally overlooked.
We are surrounded by objects made out of metal every day. Automobiles, buildings, sculptures - all contain metal in some form. steel fab near me can be an essential section of each person's life. Steel and iron are reliable and a lot more secure than wood.
This article is for those of you who will not be very familiar with metal. In this posting we will show you how metal is formed as well as show you the steps it takes for fabrication.
To start with, what does metal fabrication involve?
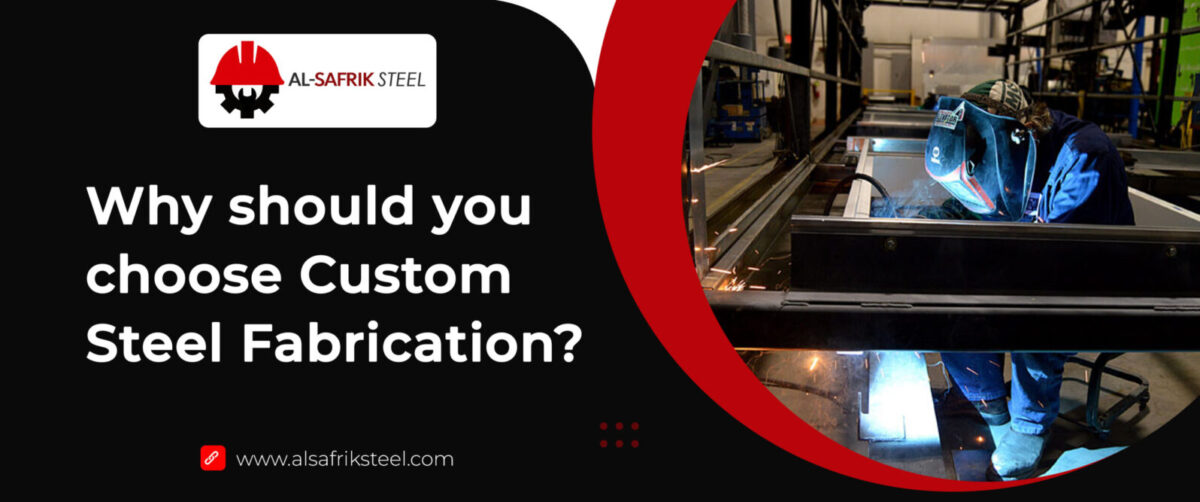
Basically, converting metal shapes into a finished product is recognized as metal fabrication. Small metal mixing bowls and giant metal cement mixing machines must all be fabricated. Metal fabrication is really a category which includes metal forming, cutting, bending, welding, and finishing.
What are the different types of metal fabrication?
The three basic types of metal fabricating are structural, industrial, and commercial. The process of manufacturing bridging and building components is known as structural fabrication. The manufacturing of processing equipment and support equipment for industrial use falls beneath the definition of industrial fabrication. The major chunk of metal items bought by consumers is produced by commercial metal fabrication.
What are the steps which are followed when the metal is cut?
Metal could be cut in two ways. A proven way is when sharp blades are rubbed up on the metal. Sometimes, though, the metal is merely completely cut out. The process of applying a great deal of pressure on a little area before metal breaks or fractures is known as shearing. It is much like a giant pair of scissors, and the process is always exactly the same. Removal of metal, however, can be achieved using varying methods including abrasives, electric arc, laser beams, or torches. They are all trusted processes for cutting metal. In the field of fabrication, abrasive wheels and cutting torches predominate because they are relatively easy to utilize and portable. Stationary equipment (e.g. water jet beds, plasma tables, and laser cutters) aren't used as much, yet they provide amazing results with precise tolerances.
To get the skills required for metal fabrication, where would you go?
Certified learning centers and face to face training are the two types of metal fabrication instruction that are most common. Either way, an individual must possess sufficient understanding of the necessary skills before they are able to obtain work in the fabrication industry. The skills of the metal working industry are maintained and promoted by several agencies like the American Welding Society, the American Institute of Steel Construction, and the American Petroleum Institute.
Like any other field, the initial stage of metal fabrication is design, the conception of an idea that will eventually lead to the finished product. When required, engineers will check that the materials used are of the strength that's needed. The fabrication facility orders materials after receiving the plans. Based on your design plan, materials will undoubtedly be cut, shaped, and welded together to make the product. Workers inspect each product before it leaves the plant to be sure it has been properly designed for its purpose.
Now you know all you need to know about metal working.